Abutment CERALOG® – innovativo e realizzato in PEKK, un polimero ad alte prestazioni
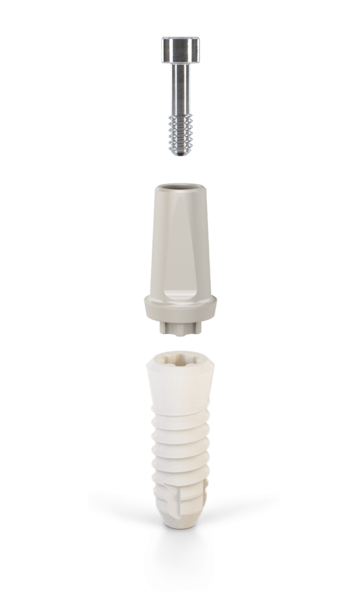
Il sistema implantare CERALOG® comprende abutment diritti e angolati realizzati con il polimero ad alte prestazioni poli-etere-chetone-chetone (PEKK). Gli abutment sono fissati nell’impianto con una vite in titanio o oro. Il PEKK è un materiale di colore chiaro ed è facilmente lavorabile con frese convenzionali.
PEKK, il polimero ad alte prestazioni
Il PEKK fa parte della famiglia dei poliarileterchetoni (PAEK), polimeri termoplastici ad alte prestazioni concepiti per applicazioni con sollecitazioni estreme e per questo impiegati in ambiti quali l’industria automotive, il settore aerospaziale e medicale. In virtù della loro struttura chimica, questi polimeri possiedono un’elevata resistenza, elasticità e stabilità all’idrolisi.
Dopo essere stato impiegato per molti anni in ortopedia, il PEKK trova ora un ampio spettro di indicazioni anche in odontoiatria. La duttilità del PEKK riduce il fattore di stress sull’impianto e simula un comportamento simile a quello dei denti naturali.
Componenti CERALOG®
Componenti CERALOG® per la gestione dei tessuti molli
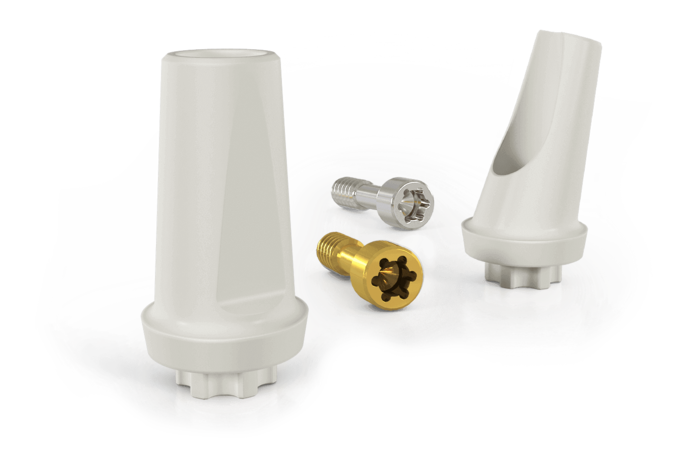
Il set dell’impianto CERALOG® include un cappuccio a vite, che viene applicato sulla connessione Hexalobe e rimane in situ per il periodo di guarigione. In via alternativa, è possibile coprire l’impianto con una vite-tappo.
Entrambi gli impianti possono essere utilizzati sia per la guarigione transmucosa che sommersa. Per il condizionamento dei tessuti molli sono disponibili cappette di guarigione in due altezze e due diametri e anche un abutment provvisorio. Questi componenti sono realizzati in PEEK e possono essere impiegati solo per un periodo di tempo limitato.
Presa d’impronta CERALOG®
La presa d’impronta degli impianti CERALOG® può essere effettuata utilizzando un transfer o una cappetta d’impronta per la tecnica sia con porta-impronte chiuso che aperto.
PEEK a confronto con PEKK
Il noto polimero ad alte prestazioni poli-etere-etere-chetone (PEEK) è utilizzato da anni in odontoiatria per ricostruzioni provvisorie, procedure di scansione e come transfer d’impronta. Anche questo polimero fa parte della famiglia dei poliarileterchetoni (PAEK). La sintesi del PEKK ebbe inizio nel 1962 a cura del gruppo chimico DuPont che, da allora, ha continuato a perfezionare il processo di polimerizzazione decennio dopo decennio.
L’ultima sintesi del PEKK è stata modificata da Oxford Performance Materials e Arkema, che hanno avviato la commercializzazione del materiale in numerosi ambiti industriali. Il grande vantaggio del PEKK rispetto al PEEK è la sua resistenza allo scorrimento più elevata e la sua resistenza alla compressione in condizioni di carico.
PEKK | PEEK | |
---|---|---|
Modulo di elasticità (GPa) | 4.5 | 4.1 |
Resistenza a trazione (MPa) | 138 | 100 |
Resistenza a flessione (MPa) | 193 | 165 |
Resistenza a compressione (MPa) | 207 | 135 |
Allungamento alla rottura (%) | >30 | 40 |
Temperatura di fusione (°C) | 360 | 340 |
Assorbimento d’acqua dopo 24 ore (%) | <0.2 | 0.5 |
Densità (g/cm³) | 1.3 | 1.3 |